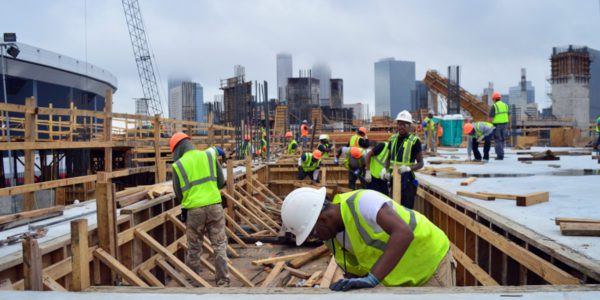
Jul 07 Georgia Construction Outlook: The Volatile Push-Pull of Material Pricing
Owners everywhere are familiar with some sort of material frustration during their projects. While it’s no secret that material pricing can trigger a surge in construction costs, the challenges of 2020 have created an extraordinary phenomenon that baffles even the most experienced Owners.
“Material procurement right now is an unprecedented challenge. Whether it’s plastics and resins, lumber, steel – across the board it’s a challenge,” says H.J. Russell & Company Vice President of Operations Michael Swick. “But right now, lumber is our biggest hot button issue.”
AN ECONOMIC WILDFIRE
A seemingly perfect storm has caused lumber prices to soar astronomically, to heights as much as 400% from this time last year. A pandemic-induced bottleneck forced Georgia sawmills to cut production early 2020, fearing a recession. Instead, demand exceeded supply. Even though the state has more trees than it has in decades, mills are struggling to cut them quickly enough to keep up. Pipeline and wholesale providers are struggling to meet demand, even going as far as to suggest that project owners and other professionals lift brand restrictions for their products.
However, much of this shortage is commodity driven. The transition of companies to remote environments produced a boom in sprawling from urban areas, increasing production of single-family homes, and at the same time, sparked a major DIY craze that drained supply from big box stores.
“There’s a lot of record construction happening, especially in the housing market, that’s flipping everything upside down. It’s anyone’s guess as to when it’ll correct itself,” says Michael.
A DOMINO EFFECT
Market volatility is also hitting cost estimators, who are struggling to give accurate pricing due to historical data that is quickly outdated. “I’ve seen a big disparity between what cost estimators are doing and the reality of the situation,” says Michael. “And that’s due to data, even a couple of months old, just not being good anymore.”
Another ripple effect of the market volatility lies within the labor market. “From what I’ve seen, it basically boils down to whoever has the lumber gets the labor. They’re getting paid by the square foot. If you don’t have what they need, they’re onto the next job site.”
A CASE FOR DUE DILIGENCE
So, does this mean Owners should buy out their projects early to lock in pricing?
That’s a very tangible thing to realize, says Michael. However, he warns that this is only contributing towards the driving hysteria and increasing demand. Much like the panic-induced toilet paper shortage of early 2020, “Owners are warehousing lumber they’ll need for the coming summer. It’s really only making the situation worse.”
The smartest thing for Owners is to look at their projects on a case-by-case basis and determine the risk tolerance of all parties. How critical are the materials to when you need them? Are you able to wait and see if prices come back down?
There’s a gray line between means and methods and design in every project. If early procurement is truly the right answer, it is important that Owners chose a GC partner early in the design process to assist with design coordination. Without proper coordination, the possibility of future changes increases exponentially. Something you may have ordered early in the project could be unusable once you get into the field and reordering that material causes costly delays and a disruption to the flow of work.
“I’ve been in the trenches with those guys, just trying to wait for the design team to get the level of detail you really need so material can be ordered,” says Michael. “We are spending a lot of time and resources to assist in design coordination to speed up the process. We are taking on that liability that has real cost in the short term, but it costs a lot less for everyone in the long term.”
THE OTP (ONE TRUE PROCUREMENT) STRATEGY
Above all else, doing your due diligence is essential. Early pre-planning and virtual coordination play a significant role in improving collaboration and construction to prevent costly mishaps down the road. As a vital part of design, preplanning and virtual coordination help safeguard expectations and the return on your investment of time, money, and resources. Those that are willing to maximize the value of technology are more likely to thrive even in the face of any uncertainty.
Still feeling uncertain among all the disruption? You’re not alone. The industry is reshaping faster than ever, and H.J. Russell is here to guide you through the impact. Let’s talk.
Contributing Writers

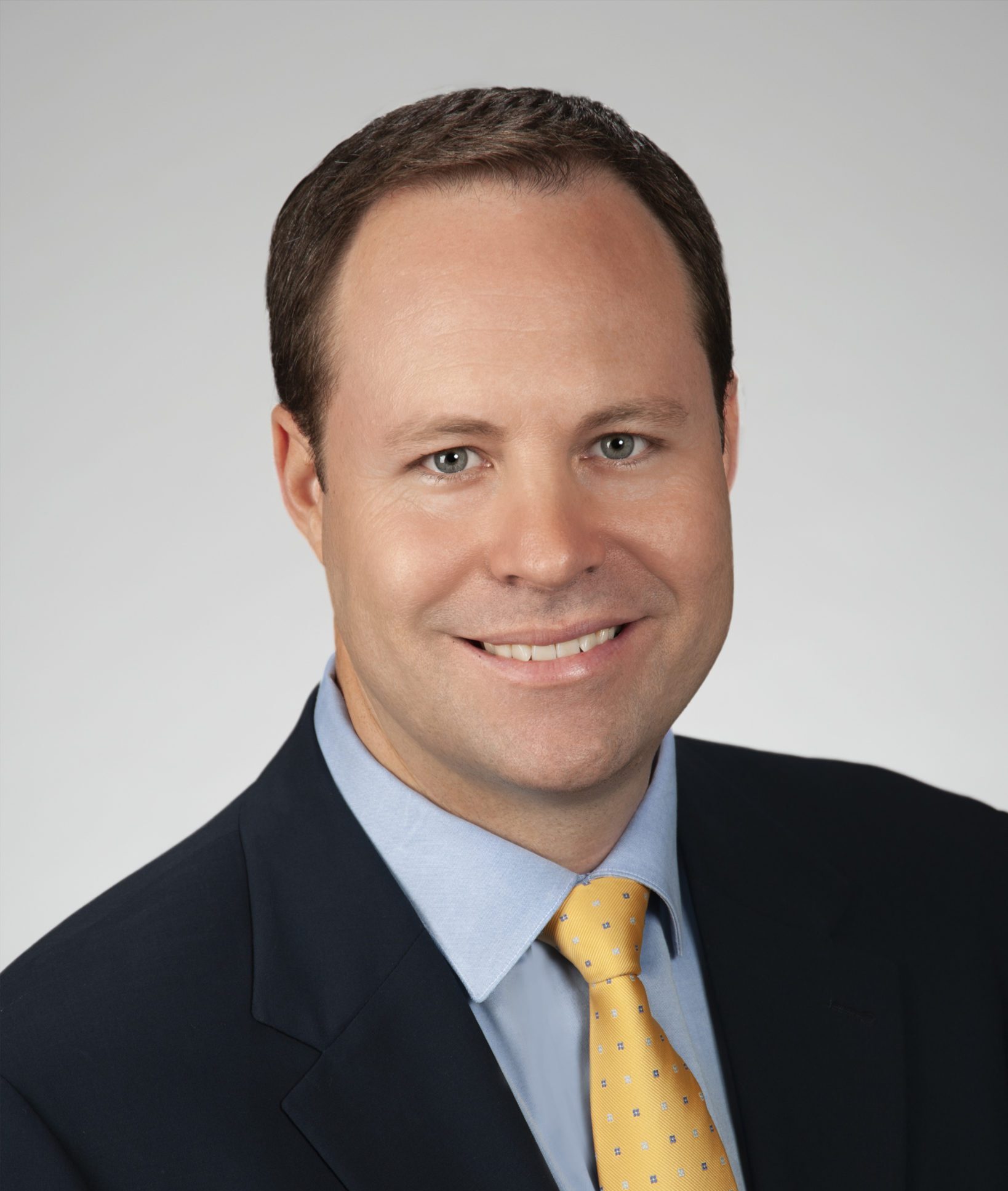
MICHAEL L. SWICK.
Vice President of Operations
Michael Swick has over 22 years of construction experience across commercial and residential sectors. He serves Vice President of Operations for H. J. Russell & Company’s construction division and is responsible for the overall leadership and growth of Russell’s construction group.
Before joining Russell, Michael was Director of Sustainability and Senior Project Manager for Choate Construction Company, a commercial general contracting firm with offices throughout the southeast and annual gross revenues in excess of $1B. As Senior Project Manager, he completed over $350M and 2.6M square feet of construction projects across a wide variety of industry sectors, including hospitality, apartment, senior living, student housing, office, warehouse, public works, athletic facilities, and retail.
Michael has held several civic leadership roles. He was elected president of the U.S. Green Building Council of Georgia in 2014 and 2015 and served as Chair of Atlanta’s Neighborhood Planning Unit-C from 2012 through 2015. He has received many awards, most notably the recipient of Engineering News-Record’s Top 20 Under 40.
Lastly, Michael studied mechanical engineering at Boston University and has an A.A.S. in construction management from Wentworth Institute of Technology. He also studied preservation carpentry at the North Bennett Street School in Boston. He is a Leadership in Energy and Environmental Design (LEED), Accredited Professional.